Introduction to Crane Remote Control
In the fast-paced world of industrial and construction environments, the need for innovative solutions to enhance operational efficiency and safety is paramount. Crane remote control systems stand at the forefront of this technological evolution, offering a leap in how we operate and manage lifting tasks. This article delves into the sophisticated world of crane remote controls, with a spotlight on the Scanreco RC400 G2B system, a pinnacle of remote control technology developed for hydraulically driven mobile cranes and machinery.
Exploring Crane Remote Control Technologies
Crane remote control systems have undergone significant transformations, evolving from simple mechanical devices to complex, microprocessor-based technologies. These systems allow operators to control cranes from a safe distance, reducing the risk of accidents and improving the precision of lifting operations. The essence of remote control operation lies in its ability to send digitally coded control information wirelessly, ensuring real-time responsiveness and control over the crane’s movements.
Detailed Overview of the Scanreco RC400 G2B Remote Control System
The Scanreco RC400 G2B represents the zenith of remote control technology, tailored specifically for the rigorous demands of hydraulic mobile cranes. This system is a marvel of engineering, featuring a portable control unit for proportional control and switches for ON/OFF functions, a central unit for driving proportional electro-hydraulic slide controllers, and compatibility with all hydraulic valve types found in today’s market.
STOP FUNCTION SWTICH
There is a red stop function switch (STOP) with a manual twist reset, a push button and a red LED on the control unit’s stop function panel, see figure 3.4. The control unit is started with the spring reset push button (9) All movement of the crane is stopped if the stop function is activated on the control unit. The red LED indicates operating and battery status.
SWITCH PANEL (ON/OFF FUNCTION)
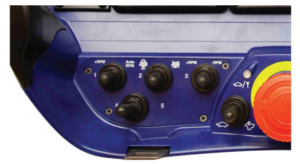
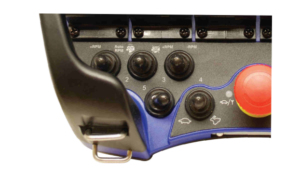
The switches on the switch panel allow actuation of digital functions via toggle switches and push buttons. digital functions can be used te manoeuvre electrical, hydraulic or pneumatic ON/OFF functions. Examples of functions:
- Stopping and starting of the vehicle’s motor, throttle lever, beep / signal, change-over valves, function changing for ex. 7:th and 8:th function, etc.
MICRO-SPEED CONTROL
This return spring switch can be used to reduce the operating speed in five (5) steps from 100% to 60%, 50%, 40%, 30% and 20% speed by limiting the hydraulic steering. The regulation of the function’s speed is still made over the entire lever stroke and with retained resolution.
- With impulses from the spring loaded toggle switch to the left, towards the turtle , speed reduction can be produced from 100% to 60%, 50%, 40%, 30% and 20% steering. Movement of the switch to the right, towards the rabbit, will produce 100% steering once again.
- For safety reasons, a return to 100% steering can only be made if all manoeuvre levers are in their zero positions.
- When the green LED is blinking, the Micro-speed function is activated. The number of blinks indicates the operating speed as defined in the table below.
If the stop function is pressed on the controller unit, the controller unit will start from the last chosen speed.
Green LED | Indication |
---|---|
not lit | 0 to 100 % speed (normal speed) |
1 blink every third second | 0 to 60 % speed |
2 blinks every third second | 0 to 50 % speed |
3 blinks every third second | 0 to 40 % speed |
4 blinks every third second | 0 to 30 % speed |
5 blinks every third second | 0 to 20 % speed |
CRANE STOP FUNCTION BOX (OPTIONAL)
Crane stop function box (optional) The crane stop function box is a separate unit for fixed mounting on the vehicle . The crane stop function box must be connected between the vehicle battery and the central unit.
- When the stop function is activated the main power supply to the entire remote control system is disconnected. « The crane stop function must be suitably located and easily accessible.
- Before operation is started, the driver must inform all fellow-workers about the stop function and its location.
- Crane stop function box is not a scope of delivery from Scanreco – it is the installers responsibility. With the central unit switch in MANUAL position and an electric dump valve, the stop function is also available during manual hand lever operation.
Benefits of Using Crane Remote Control
Adopting crane remote control systems like the Scanreco RC400 G2B brings numerous advantages, including enhanced safety by maintaining a safe distance from the load and operational area, improved operational efficiency through precise and quick maneuvering, and increased precision, which is crucial for complex lifting tasks.
Palfinger Crane Remote Control. Thanks to remote control operator can safely operate machine from a distance. SOURCE
Technical Specifications of the Scanreco RC400 G2B
This system excels in providing smooth control over typical proportional functions such as slewing, main lift, jib extension, and more. Its design is focused on ease of use, safety, speed, and precision, supported by an electronic core that is highly configurable to meet various operational needs.
Item | Technical data |
---|---|
Supply voltage | 12 VDC / 24 VDC (+/- 20% / max. 5% V peak to peak) |
Internal fuse | Plus: + 10 Amp. (Standard car fuse / Red) |
Max. over-voltage | Approximately 33 VDC (Fuse blows) |
Proportional functions | 1 - 8 double operating proportional functions |
Dump valve drive | Max. 2.0 Ampere (short circuit proof) |
ON/OFF drive | Max. 1.8 Ampere (short circuit proof) |
Regulation signals | Voltage or PWM (Other upon request) |
Current consumption at idle | 40 mA |
Weight | 1.20 Kg (Valve and connection cables not included) |
Dimensions (WxHxD) | 227x205x78 mm |
IP Class | IP65 |
Ambient temperature (Celsius / Fahrenheit) | -25°C to +70°C / approx. -15°F to +160°F |
Application Scenarios for Crane Remote Control
From construction sites to industrial settings, the Scanreco RC400 G2B system finds its application wherever there is a need for precise, safe, and efficient crane operations. Its versatility makes it suitable for a range of cranes, including but not limited to HIAB, JONSERED, and PALFINGER.
Installation and Setup of the Crane Remote Control System
Installing the Scanreco RC400 G2B system is straightforward, requiring integration with the crane’s hydraulic system. The system’s design ensures it can be easily set up and calibrated, providing a user-friendly interface for operators to adjust settings according to specific job requirements.
Operational Guidance for the Scanreco RC400 G2B
Operators will find the Scanreco RC400 G2B system intuitive and adaptable. The portable control unit’s levers and switches are designed for ergonomic and fatigue-free operation, offering precise control over crane movements. The system also includes features such as multi-step micro-speed operation for nuanced control and a comprehensive array of switches for ON/OFF functions.
Maintenance and Troubleshooting
Routine maintenance is simplified with the Scanreco RC400 G2B, ensuring long-term reliability and performance. The system is equipped with diagnostic features for easy troubleshooting, minimizing downtime and maintaining operational efficiency.
Comparative Analysis with Other Crane Remote Control Systems
When compared to other systems in the market, the Scanreco RC400 G2B stands out for its durability, versatility, and precision. Its compatibility with various hydraulic valves and comprehensive control options make it a superior choice for a wide range of applications.
Conclusion and Final Thoughts
The Scanreco RC400 G2B crane remote control system embodies the future of lifting operations, offering a blend of safety, precision, and efficiency that is unrivaled in the industry. As technology advances, crane remote control systems will continue to play a crucial role in enhancing operational standards and safety in construction and industrial settings.